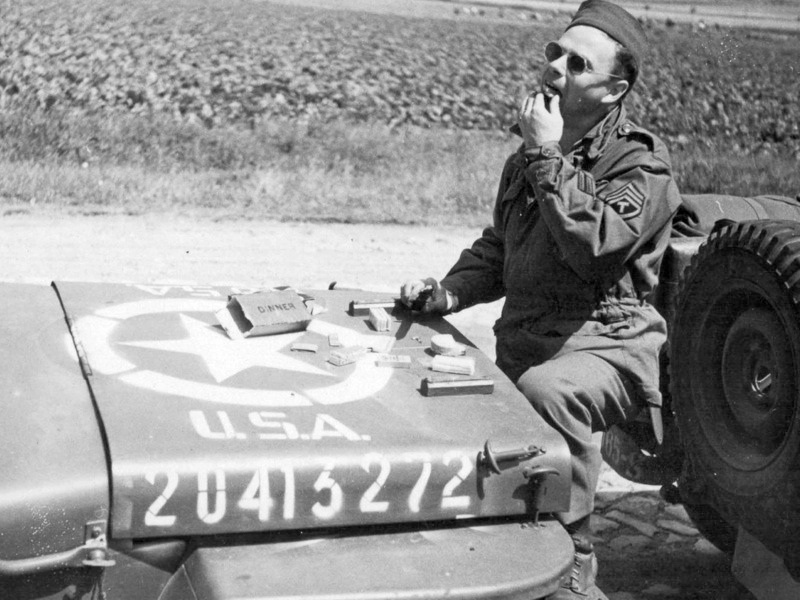
The whole unit is packed snugly in an inner carton measuring 3 14/32 x 1 14/32 x 6 20/32 inches, made of kraft-lined fiberboard, and sealed with waterproof glue. The carton is wax-dipped twice […]. To keep the waxed boxes from sticking together, they are enclosed in smooth, unwaxed cartons.
Early, experimental, K Rations consisted of three individual cardboard boxes in which the packages of the foodstuff was packed. These boxes were dipped in wax to seal it against gas and to make the box waterproof.
When the K Ration went into full production, six types of waterproofing methods were specified in May 1942. Each prime contractor would waterproof the rations, using a synthetic wax, as stipulated in the contract. The method of waterproofing depended on the capabilities of the company. The type VI method, however, seems never to have being used.
Type I: The carton is coated inside and outside with wax. The printing will be on the box.
Type II: The carton will be dipped in molten wax, then overwrapped with waxed kraft paper and then dipped again in molten wax. The printing will be on the waxed paper.
Type III: The (inner) carton will be dipped in molten wax and then inserted into a snugly fitting (outer) carton. The printing will be on the outer carton.
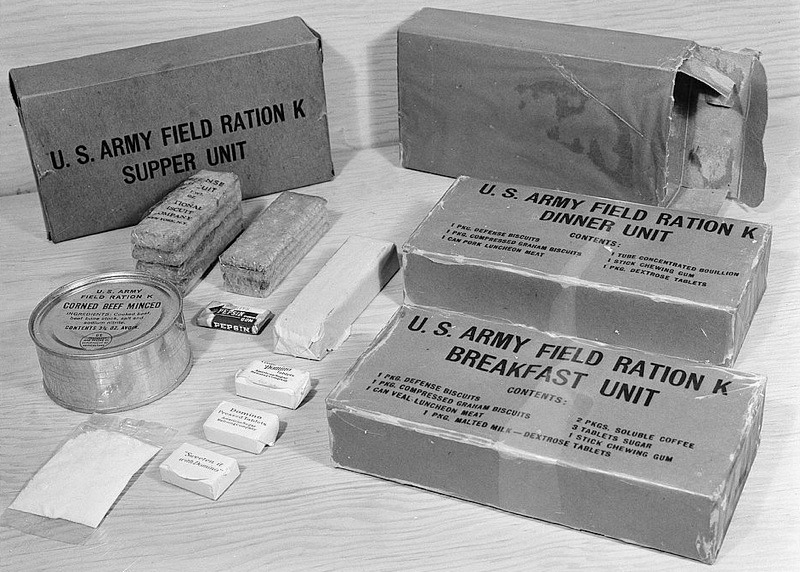
This official photo is misleading that it is showing two different types of cartons. On the right are shown two early type II units in waxed (overwrapped) cartons. In the back are the Type III outer carton with opened inner carton (this is a tuck in carton overwrapped and waxed), with the contents layed out on the left.
Type IV: The carton is of a telescoping type, wrapped with adhesive waxed kraft paper making complete contact with all surfaces of the carton. The carton then will be dipped in molten wax and overwrapped again with waxed kraft paper. The printing will be on the outer waxed paper.
Type V: All components are sealed inside a laminated cellophane bag. This bag is placed in a telescoping carton that is overwrapped twice with waxed kraft paper. The seams of the wrappings are opposite of each other. The outer wrapping bearing the printing.
All cartons have an inside dimension of 3 13/32" wide, by 1 13/32" high, and 6 19/32" long.
Type VI: The container constitutes of a square fiber body can (with rounded corners) that is coated inside and out with wax and is closed with black metal ends. A printed kraft paper label will cover the body of the fiber can completely.
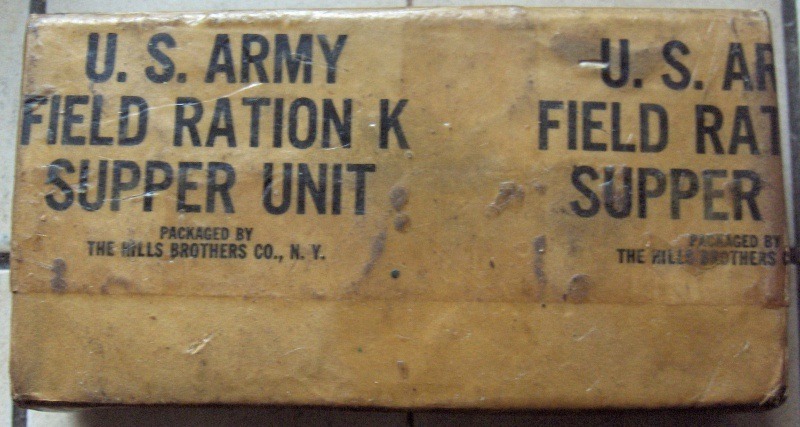
A Supper unit packed by The Hills Brothers Co., using a waxed paper wrapping that has been printed in a repetative pattern.
It was found that the waxed units would stick together when stored in warm climate. To prevent sticking, type III was preferred, or if the inner carton was wrapped in waxed paper it was inserted in an outer carton. From now on a distinction was made between the inner carton and outer carton. Early productions appears to be Type IV. Later the Type III appears to be the preferred type.
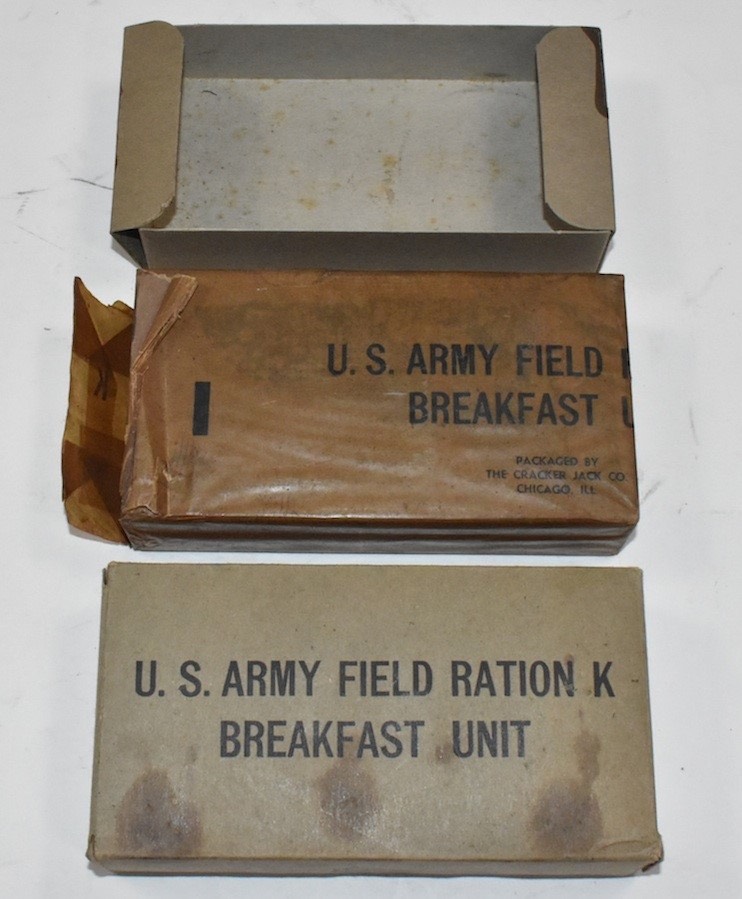
This is what appears to be the first type of packaging (Type IV) used when the K ration was procured in greater numbers. This type was mainly used during training and field tests to test the new K Ration. (photo: 1944Supply)
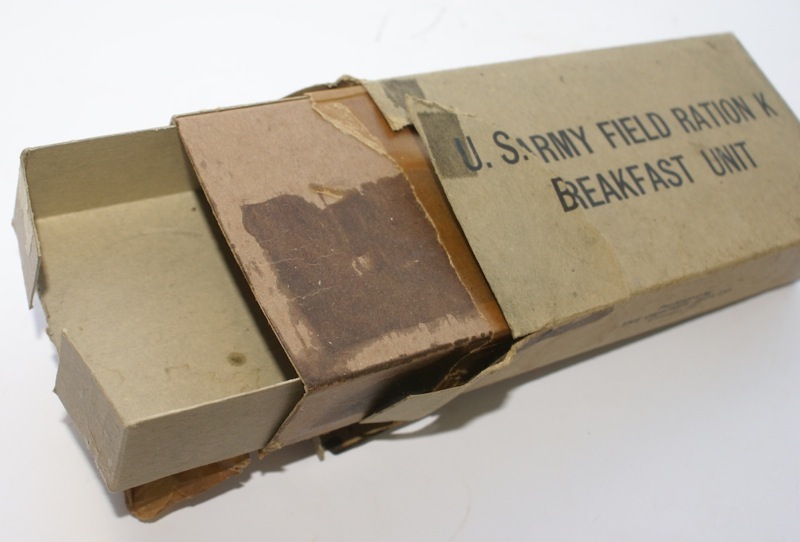
Note how the tray fits inside a cardboard sleve, then both are overwrapped with waxed paper. The whole packaging then is protected by the outer carton with tuck in flaps. This method of packaging is what is reffered to as the telescoping type. (photos: 1944Supply)
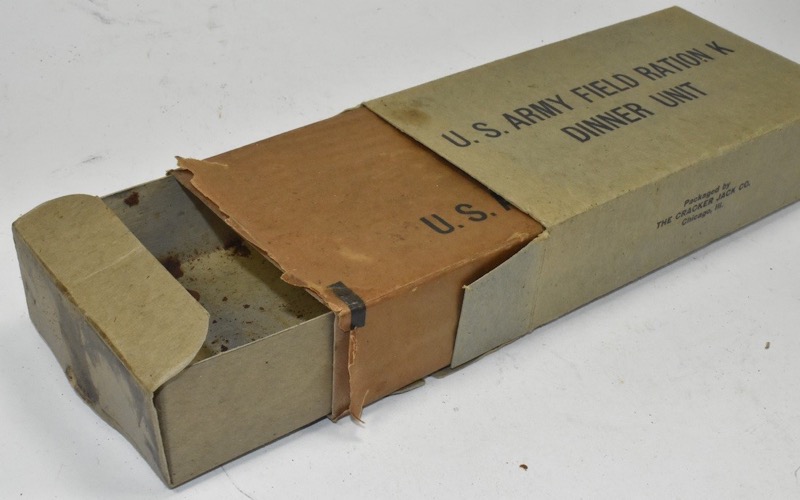
Here's a still from the "Food for Fighters" film (1943). Clearly can be seen the trays on the conveyor belt that are being filled with the separate components, chewing gum is just being placed on top of the biscuits. Next, the can is placed towards the open end of the tray. Note that the workers are black women (cheap labor!) and that the equipment is crudely made from wooden boards.
An alternative found with the early production is that the inner carton is wrapped twice with waxed paper and then inserted in the outer carton. Since the first wrapping sticks completely to all surfaces of the inner carton, it appears that the inner carton might be waxed as well.
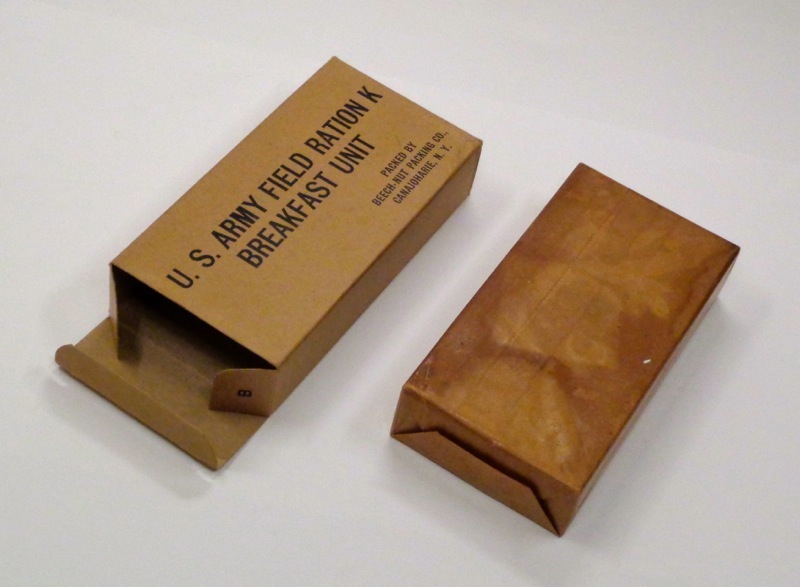
A Beech-Nut produced Breakfast unit's inner carton that is only overwrapped twice with waxed paper, then inserted in an outer carton. The outer carton is dated 12-42.
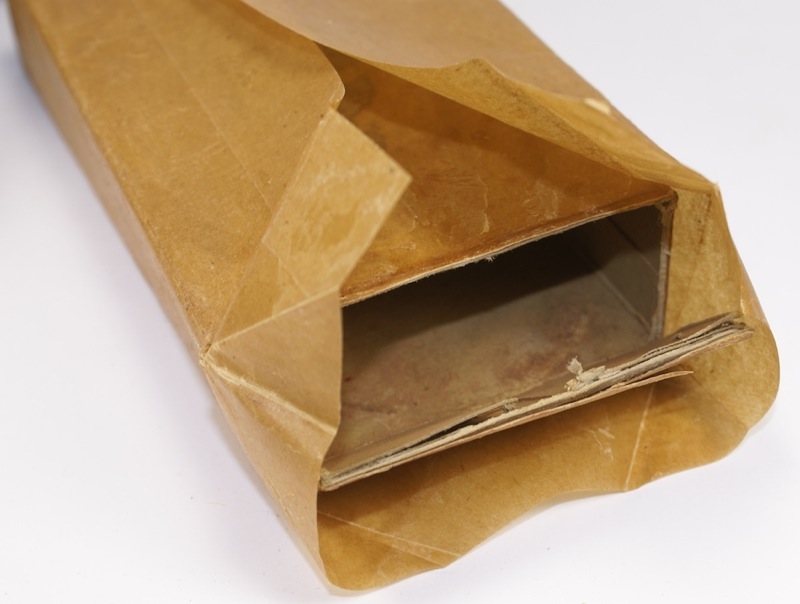
A close up of a Chicle produced Breakfast unit shows the double wrapping with waxed paper. The first wrapping is stuck firmly to the inner carton with the second wrapping folded loosely around it, with the seam opposite of the first layer. (photo: 1944Supply)
For identification purpose the outer carton was printed, as prescribed earlier in the outer carton chapter, but it was left to the packer whether or not the inner carton needed to be marked for identification on the production line. Early on some contractors didn't deemed it necessary to mark the inner cartons, others simply used the same printing as used on the outer cartons.
Later in the war it became more common to mark the units with "BREAKFAST UNIT", "DINNER UNIT" or "SUPPER UNIT", or just "BREAKFAST", " DINNER" or "SUPPER".
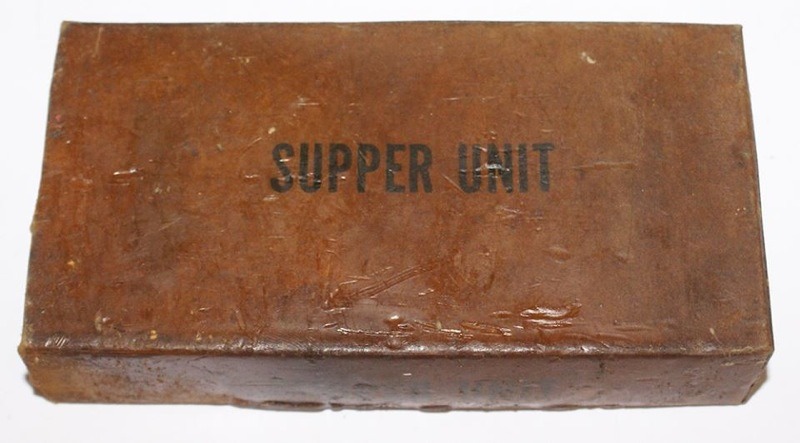
"SUPPER UNIT", this is the most used type of printing on the inner cartons for identifying the units. The thick layer of wax, a result from the double dipping, can be clearly seen on this example. (photo: 1944Supply)
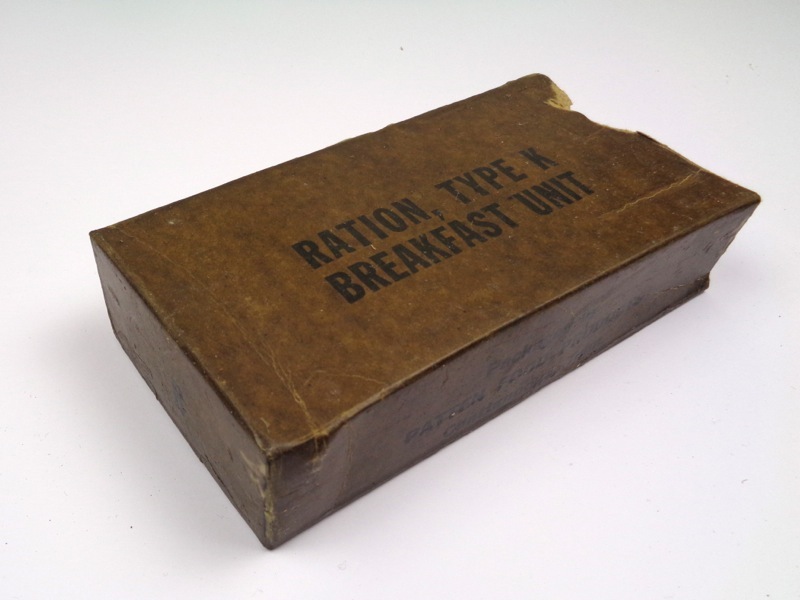
Some contractors used the complete nomenclature on the inner carton. This Patten Food Products Breakfast unit has the nomenclature printed only on one main panel.
The wax used for dipping is a synthetic compound with a melting point higher than 140°F and will not crack or chip at -20°F. It should not be sticky at 120°F. The wax is odorless, tasteless and non-toxic.
The waxed inner cartons all have a brown appearance. This is not caused by the color of cardboard used, but the wax itself has a brown hue. The color for the wax is set at a maximum 240 within the Red 500 Series of the Lovibond scale. (This is a color scale for liquids.)
Usually the dipping is done twice. The first dipping was done at approximately 190°F for 5 to 10 seconds to impregnate the cardboard. After a cooling period a second dipping is done with wax of a slightly lower temperature to coat the carton with a uniform protective overall coating.
A waxed carton should withstand immersion for 20 hours.
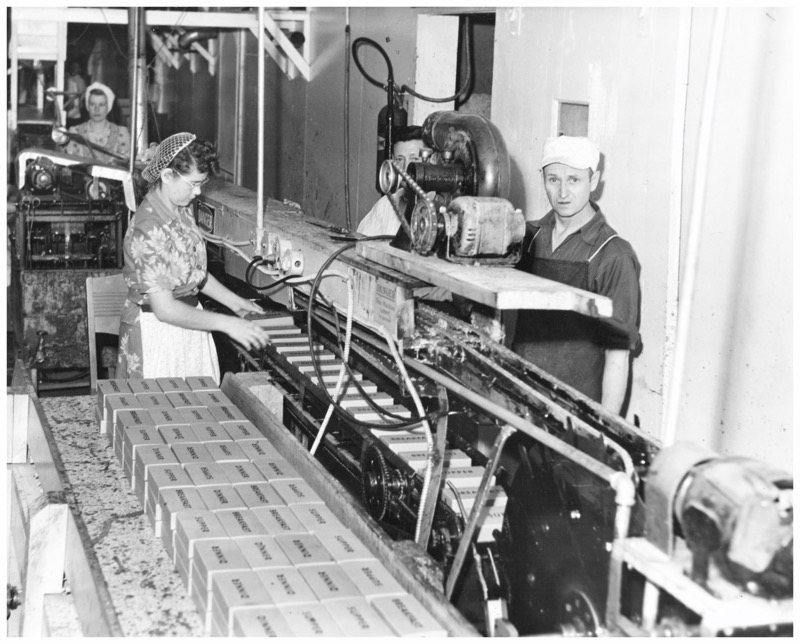
K Ration units are placed on the convayer belt of a wax dipping machine at a prime contractor in New Richmond, Wisconsin (6-28-1944).
Note that all three types of units are being waxed. This is why the inner cartons are labeled, so that after dipping all units are placed in their corresponding outer cartons.
Occasionally the inner cartons were marked with an embossing or imprint showing the name of the unit or just the letter "B", "D" or "S".
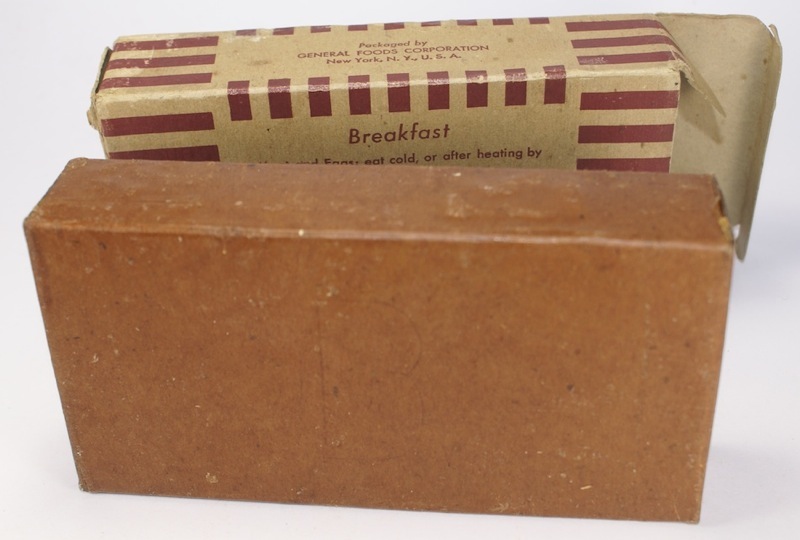
A large imprinted "B" can be seen faintly to identify the unit as a Breakfast.
When the can was inserted into a cardboard sleeve, the inside dimensions of the inner carton was increased to 3 16/32" x 1 16/32" x 6 26/32" to allow for more room.
In specifications of 1945 five methods of waterproofing are described. These methods not only refer to the waterproofing of the inner cartons, but also to the final packing in the shipping case. After waterproofing, all inner cartons are placed in an outer carton.
Waterproofing method I, II and III are all three the same, but difference is made according to the final packing of the shipping cases. Method I, IV and V are packed in a fiberboard box. Method II and III are packed in a corrugated box that is placed inside a kraft paper laminate bag, both methods using a different style of bag. (see the SHIPPING CASE chapter)
Method I, II and III: The inner carton will be dipped in molten wax, and after cooling down dipped again in slighly cooler molten wax for an overall coating.
Method IV: The inner carton is wrapped in a triple ply laminated sheet made of one layer each of sulphite paper, aluminum foil and kraft paper. This laminated sheet is waxed on the outside and, when wrapped, the seams are heat sealed. A second wrapping of waxed kraft paper is applied with its main seam opposite of the first wrapping.
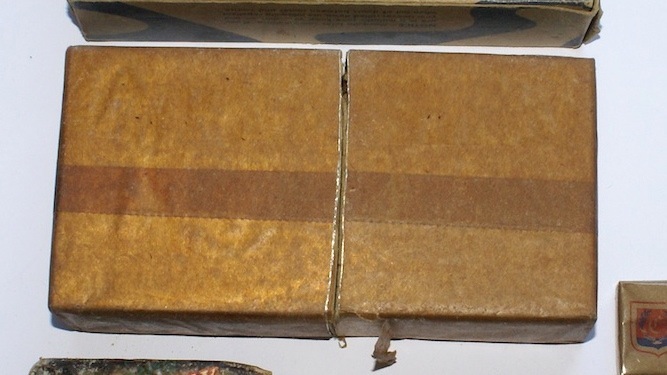
A method IV inner carton has been cut in half, showing clearly the aluminum foil laminate. The dark band is from the overlapping waxed paper overwrap. (photo: 1944Supply)
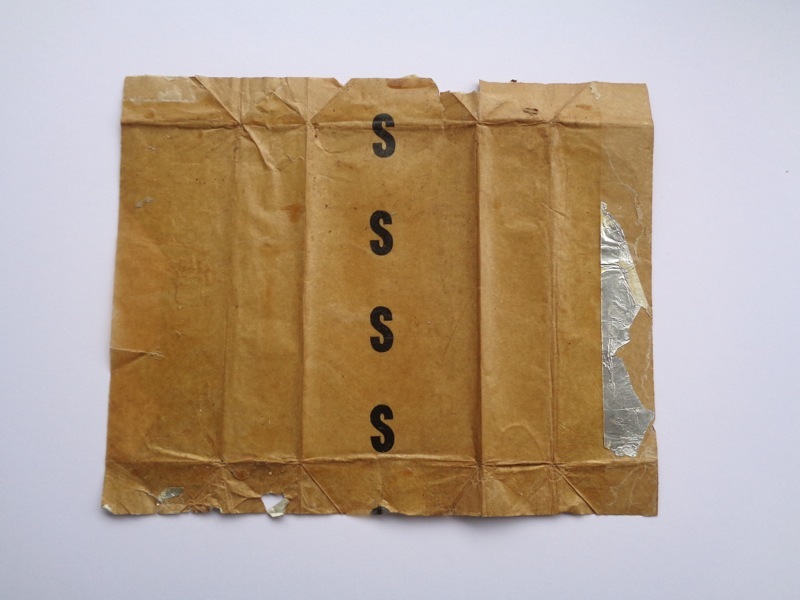
A method IV laminated inner carton wrapping that has been printed with an "S" to indicate it is a Supper unit. The laminated wrapping was produced on a roll with a repeating "B", "D" or "S" printed along its entire length.
The picture above shows the kraft side and the aluminum foil side is shown below.
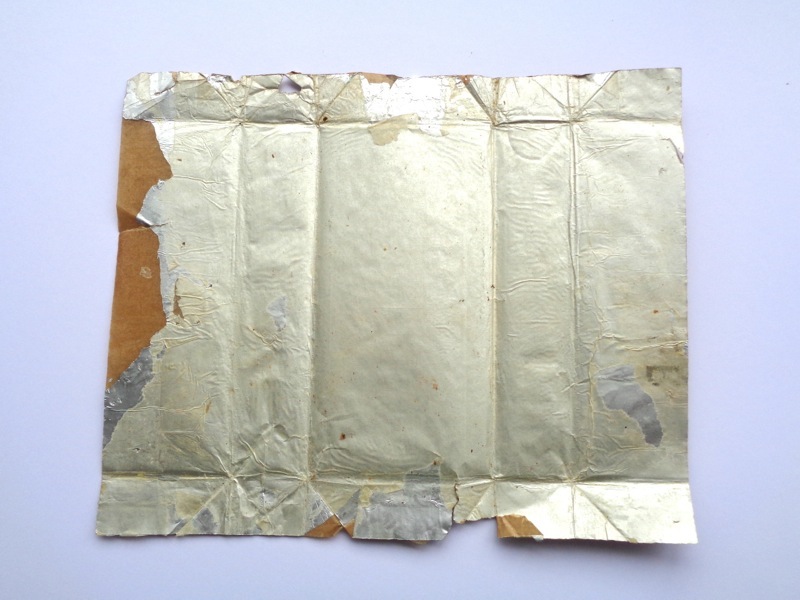
Method V: The inner carton is wrapped with the same laminated sheet as described in method IV, but instead of a second wrapping the carton will be dipped in molten wax.
The first method (I, II and III) is prevalent.
Cellophane bag
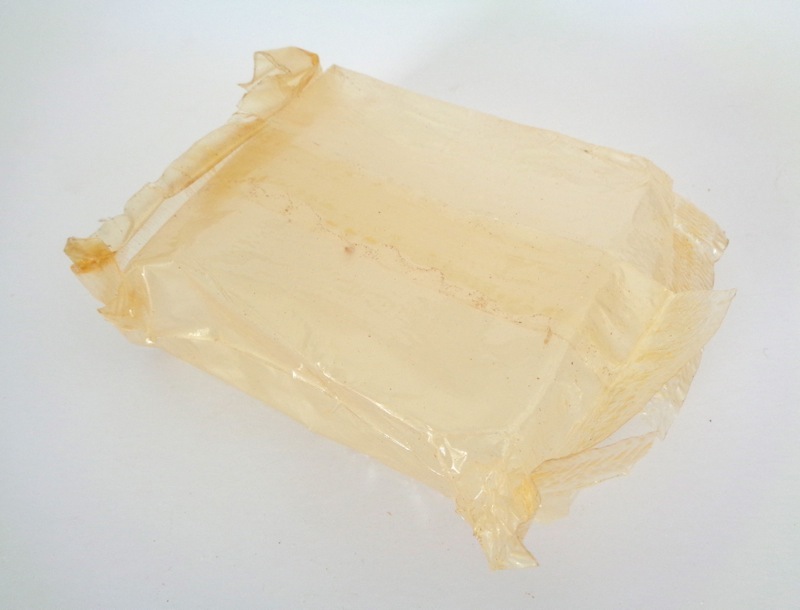
All food products, except the canned egg, cheese or meat product and the chewing gum, were sealed inside a cellophane bag for further protection against moister. Originally the contents were packed loose in the box, but when the K Ration went into full production a cellophane bag of single thickness was used to enclose the biscuits, sugar, confection and beverage.
![cellophane bag with contents]](_Media/cellophane-bag-with-content_med_hr.jpeg)
A cellophane bag with its contents from an early 1944 Breakfast unit.
With the early packages it was found that the cellophane bag would crack or tear where the confection (3 15/16" long) protruded. To prevent this all confections were to be not longer then 3 1/8 inch long.
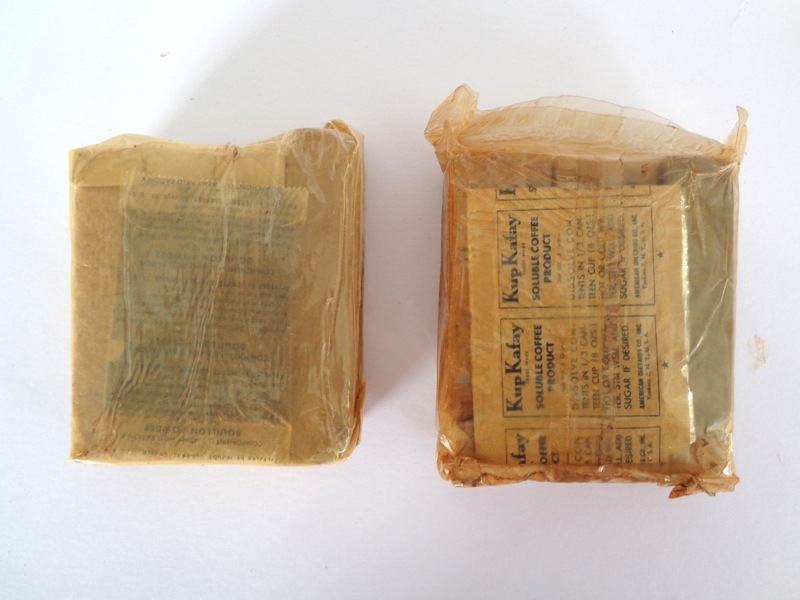
Left: an early Supper package with the longer D-bar protruding past the three sugat tablets. Right: a Breakfast package with a fruit bar of 3 1/8" length, making it a neat rectangular package. There is enough room for a row of four sugar tablets across the bottom of the cellophane bag.
Further development on the protective qualities of the K Ration packaging led to experimentation of different types of bags. Cellophane laminated to aluminum foil or kraft paper, or a lead foil laminated to paper were tried, but not deemed durable. A new bag made of a two ply cellophane (cellophane laminated to cellophane) was standardized as the only acceptable type of packaging in 1943.
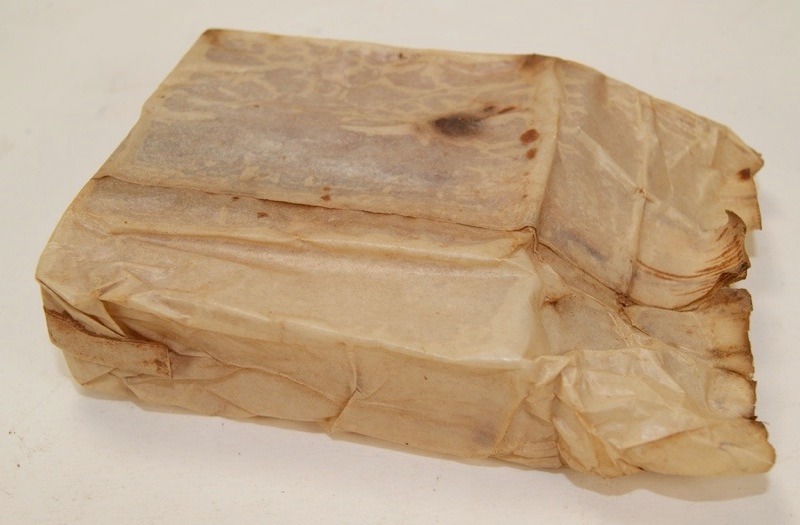
A bag from a 1942 K Ration packed by the Cracker Jack Company. It appears to be made of glassine laminated to cellophane. (photo: 1944Supply)
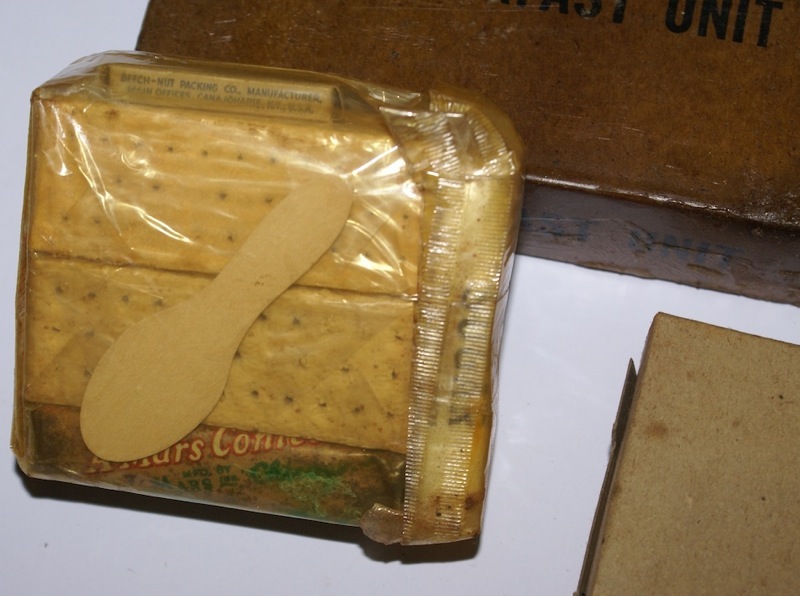
Candy coated Beechies chewing gum is included inside the cellophane bag of this 1945 Dinner unit. (photo: 1944Supply)
The chewing gum was not to be included inside the bag because the flavor could impart the other components. Only when later in the war candy coated chewing gum became available again it was allowed to be included inside the cellophane bag. Usually the K Rations produced in 1945 have the candy coated chewing gum.